Lifting Equipment Regulations: Ensuring Compliance and Safety in the Workplace
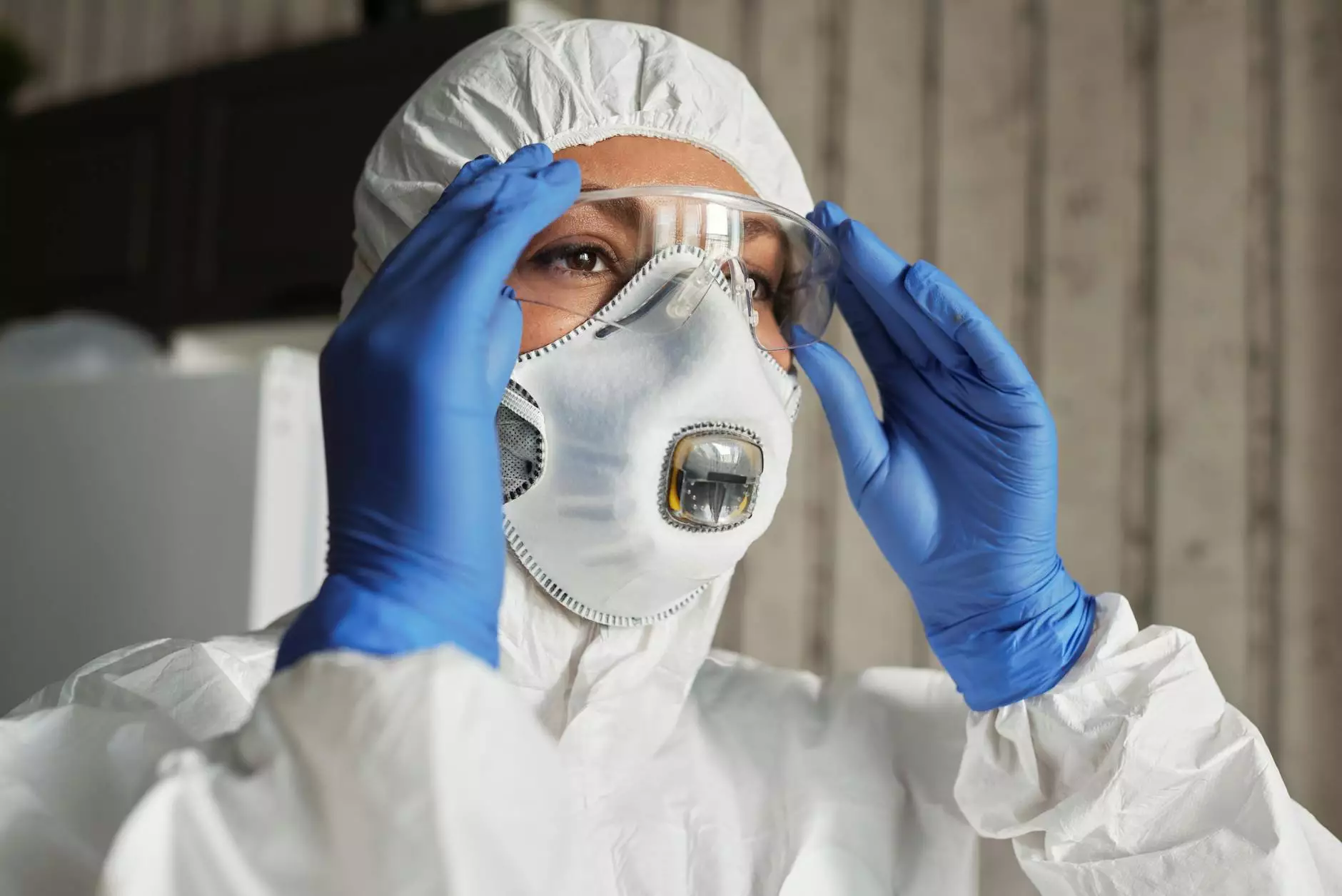
In today's fast-paced industrial environment, understanding lifting equipment regulations is crucial for maintaining workplace safety and efficiency. Regulations outline essential standards that organizations must adhere to while operating various types of lifting equipment, from cranes to forklifts. This article delves deeply into the intricacies of lifting equipment regulations, providing comprehensive insights on definitions, compliance standards, inspection protocols, operator requirements, safety practices, and the importance of documentation.
1. Understanding Lifting Equipment
To navigate the lifting equipment regulations effectively, it's imperative to first clarify what constitutes lifting equipment. According to various regulatory frameworks, lifting equipment can be defined as:
- Cranes: Large machines that lift and move heavy materials.
- Forklifts: Vehicles equipped with a pronged device to lift and transport goods.
- Hoists: Devices that use electric or manual power to lift loads vertically.
- Slings: Straps that secure loads during lifting operations.
Furthermore, operators of lifting equipment must be adequately trained and certified. Understanding these definitions helps organizations identify the apparatus subject to regulatory scrutiny, ensuring compliance with both safety and legal standards.
2. Standards and Compliance
Several regulatory bodies oversee the compliance of lifting equipment regulations, with prominent standards set by organizations such as the Occupational Safety and Health Administration (OSHA), the American National Standards Institute (ANSI), and industry-specific standards applicable in various nations. These organizations publish guidelines that outline safe operating procedures and performance criteria for lifting equipment.
Key Regulatory Frameworks
- OSHA: Sets forth mandatory safety guidelines to protect workers from lifting-related hazards.
- ANSI B30 Series: Comprehensive guidelines covering various types of cranes and lifting equipment.
- ISO Standards: International standards that provide global compliance guidelines.
Compliance with these standards not only enhances workplace safety but also mitigates legal risks and promotes operational efficiency.
3. Inspection and Maintenance Protocols
Regular inspection and maintenance of lifting equipment are critical components of lifting equipment regulations. These protocols ensure that all machinery remains in safe working condition, reducing the risk of accidents caused by equipment failure. The following guidelines summarize best practices:
Inspection Guidelines
- Daily Inspections: Operators should conduct a visual inspection before the commencement of daily operations, checking for any visible signs of wear or damage.
- Periodic Inspections: In addition to daily checks, thorough inspections should be performed at intervals defined by regulatory standards, typically at least annually.
- Load Testing: Routine load tests should be executed to validate the lifting capacity of equipment, ensuring safety margins are met.
Maintenance Practices
Effective maintenance practices include:
- Scheduled Maintenance: Establish maintenance schedules based on the manufacturer’s guidelines and regulatory requirements.
- Record Keeping: Maintain detailed logs of all inspections, repairs, and maintenance activities.
By adhering to these protocols, organizations can significantly enhance the reliability and safety of their lifting operations.
4. Operator Requirements
One of the pivotal aspects of lifting equipment regulations is the requirement for qualified and trained personnel. Operators must possess specific qualifications to ensure they can handle the equipment safely.
Training Requirements
- Certification: Operators must complete a recognized training program and obtain certification demonstrating their competency in using lifting equipment.
- Safety Training: Operators should receive training in safety protocols and emergency procedures specific to lifting operations.
- Ongoing Education: Continuous education and recertification help keep operators updated on the latest safety standards and regulations.
5. Use and Safety Protocols
Operating lifting equipment safely is paramount, not only for the operator’s well-being but also for the safety of all personnel on-site. Safety protocols outlined in regulations provide a framework for safe operation.
Best Practices for Safe Operation
- Pre-Operational Checks: Perform all necessary checks and inspections prior to use.
- Environmental Conditions: Assess and ensure that environmental conditions (weather, space) are suitable for lifting operations.
- Clear Communication: Establish clear communication protocols among team members, especially when conducting lifts in team environments.
- Load Management: Respect the load limits of the equipment, and never exceed the manufacturer's specified weight capacities.
- Emergency Procedures: Train all personnel on emergency procedures, including evacuation plans and equipment shut-off strategies.
Implementing these protocols can dramatically reduce the chance of accidents and create a culture of safety within an organization.
6. Reporting and Record Keeping
Documentation is a vital element of lifting equipment regulations. Accurate reporting and record-keeping not only demonstrate compliance but also enhance accountability in safety management.
Essential Documentation Practices
- Inspection Records: Maintain detailed logs of all inspections, including dates, findings, and corrective actions taken.
- Maintenance Logs: Document all maintenance activities, tracking work performed and parts replaced.
- Incident Reports: Keep records of any incidents or accidents involving lifting equipment, including the nature of the incident and actions taken post-event.
- Training Records: Document all operator training and certifications, including dates of completion and topics covered.
These records play a crucial role in ensuring compliance with regulatory standards and can be invaluable in case of audits or investigations related to workplace safety.
Conclusion
In conclusion, understanding and adhering to lifting equipment regulations is essential for ensuring safety in the workplace. By familiarizing yourself with the definitions, compliance standards, inspection protocols, operator qualifications, safety practices, and documentation requirements, organizations can effectively manage risks associated with lifting equipment. Not only does this enhance operational efficiency, but it also fosters a culture of safety that protects workers and promotes a positive work environment.
For businesses like Safe Plant UK, incorporating rigorous compliance practices not only meets legal obligations but also sets a benchmark for industry standards in safety and reliability.