Understanding Impulse Tube Fittings
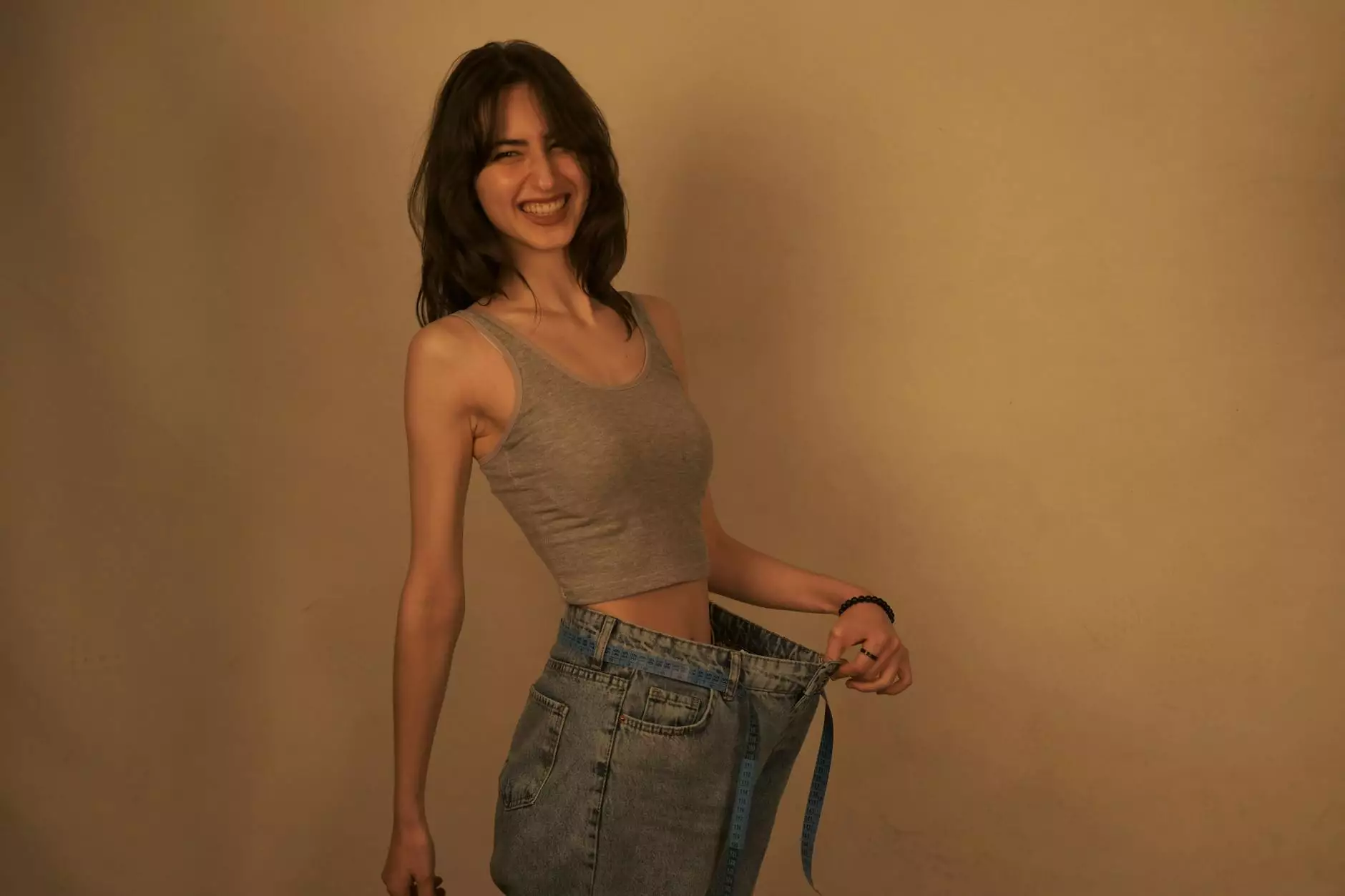
In the realm of modern industrial applications, impulse tube fittings play a pivotal role in ensuring safety, efficiency, and reliability. As a specialized category within the broader spectrum of tube fittings, these components are designed to withstand high pressures and rapidly changing conditions. This article aims to delve deep into the essence of impulse tube fittings, exploring their types, advantages, and applications, while also highlighting why they are indispensable in various industries.
What Are Impulse Tube Fittings?
Impulse tube fittings are engineered products used to connect various components within a tubing system. They are specifically designed to handle not only high-pressure environments but also to provide leak-tight seals that are crucial for maintaining system integrity. The precision engineering behind these fittings ensures that they can endure sudden pressure surges, making them essential in applications where a rapid response to pressure fluctuations is required.
Key Characteristics of Impulse Tube Fittings
- High Pressure Resistance: Designed to withstand extreme pressure levels, making them suitable for rigorous environments.
- Leak-Proof Reliability: Engineered to provide a secure and tight seal, preventing fluid leaks.
- Material Durability: Often crafted from robust materials like stainless steel and brass, ensuring longevity.
- Versatile Compatibility: Able to connect with different types of tubes and fittings, enhancing system flexibility.
The Importance of Tube Fittings in Industrial Applications
Tube fittings, including impulse tube fittings, are essential components in a range of industrial applications where fluid and gas transportation is critical. From chemical processing to oil and gas extraction, the reliability and efficiency of these fittings can directly impact operational success. Below are key sectors that benefit from high-quality impulse tube fittings:
1. Chemical Processing Plants
In chemical processing, the potential for pressure build-up during reactions necessitates robust fittings that can handle varying pressures safely. Impulse tube fittings help manage these scenarios by providing secure connections, thus preventing hazardous leaks that could jeopardize worker safety and environmental standards.
2. Oil and Gas Industry
The oil and gas sector often involves the transportation of substances under high pressure. Here, the use of impulse tube fittings ensures that there is no compromise on safety, maintaining operational efficiency while safeguarding against catastrophic failures.
3. Pharmaceutical Manufacturing
In pharmaceutical manufacturing, where contamination is a major concern, the reliability of impulse tube fittings is crucial. These fittings must maintain a sterile environment throughout the transportation process, ensuring that the integrity of the products is not compromised.
Comparing Different Types of Tube Fittings
While impulse tube fittings are vital, it's essential to understand how they fit into the broader category of tube fittings available in the market. Below is a comparison of various tube fitting types, highlighting the unique advantages of impulse tube fittings.
Ferrule Fittings
Ferrule fittings use a ferrule to create a secure seal around the tube. While they offer ease of installation and are commonly used, they may not withstand as high pressures or temperature variations as impulse tube fittings.
Forged Pipe Fittings
Forged pipe fittings are strong and durable; they are often used in high-pressure applications. However, they generally lack the rapid pressure-response capability found in impulse tube fittings, which are essential for fluctuating conditions.
Threaded Pipe Fittings
Threaded fittings depend on screwing mechanisms to secure the connection. They are versatile but can be prone to leaks under high pressure, unlike the leak-proof design inherent in impulse tube fittings.
Choosing the Right Impulse Tube Fitting
Selecting the appropriate impulse tube fitting for your application involves several considerations:
- Material Compatibility: Ensure that the material of the fitting is compatible with the fluid or gas it will handle.
- Pressure Ratings: Evaluate the pressure requirements of your system to select a fitting that meets or exceeds these specifications.
- Temperature Tolerance: Assess the temperature range of your application to prevent failure or leakage.
- Connection Type: Consider whether you need a specific type of connection, such as welded or threaded, and how it will integrate with existing systems.
Benefits of Using Impulse Tube Fittings
The use of impulse tube fittings offers numerous benefits, simplifying operations and ensuring reliability in high-stakes environments:
1. Enhanced Safety
The primary benefit of impulse tube fittings is their ability to significantly enhance safety in high-pressure systems by preventing leaks and failures.
2. Increased Efficiency
These fittings streamline fluid handling processes, reducing the potential for downtime caused by leaks or system failures.
3. Cost-Effectiveness
By minimizing leaks and system failures, businesses can save on maintenance and repairs, enhancing their overall operational efficiency and cost-effectiveness.
4. Versatility in Use
Impulse tube fittings can be adapted for use in various environments, making them suitable for multiple industrial applications.
Best Practices for Installing and Maintaining Impulse Tube Fittings
To ensure that impulse tube fittings function optimally throughout their service life, adherence to best practices during installation and maintenance is essential:
Installation Guidelines
- Always clean the tubing ends before installation to remove any debris.
- Ensure that the fittings are compatible with the tubing material and diameter.
- Follow strict torque specifications to avoid over-tightening, which can lead to material failure.
- Inspect the fittings regularly during installation to confirm correct alignment and positioning.
Maintenance Tips
- Conduct regular inspections to check for signs of wear or leaks.
- Perform pressure tests periodically to ensure the integrity of the fittings.
- Replace any damaged fittings immediately to avert potential system failures.
- Keep records of maintenance and inspections to track the performance of the fittings over time.
Conclusion
In conclusion, impulse tube fittings are a vital component in the architecture of modern industrial applications. Their unique ability to withstand challenging conditions while providing safe and reliable connections cannot be overstated. As we move forward in an era that increasingly demands efficiency and safety, understanding the importance of these fittings is crucial for businesses in sectors ranging from chemical processing to pharmaceuticals and beyond. By choosing the right component, such as those offered by TechTubes, industrial operators can ensure not only optimal performance but also contribute to safer working environments.
Explore More at TechTubes
At TechTubes, we specialize in providing high-quality tube fittings, including impulse tube fittings, to meet your industrial needs. Browse our comprehensive catalog to discover solutions that enhance safety, reliability, and efficiency in your operations.